Injection molding can produce high quantities of plastic products at an affordable cost. Molten plastic flows from the injection unit into a mold via a sprue and runner channels. This allows one mold to create several different products.
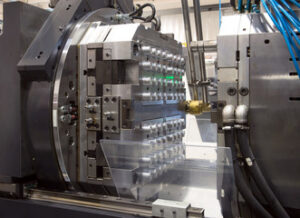
Injection molding has many benefits, including low production cost and consistent part tolerances. But it also comes with its own set of challenges. Read on Plastic Mold Injection Process Florida for more details.
Injection molding uses certain kinds of plastics called thermoplastics. These plastics melt to a liquid or moldable state at high temperatures, and then harden into the final shape of the finished product after cooling. Thermoplastics can also be reshaped repeatedly without losing their original properties, which makes them ideal for many applications. Thermoplastics are much more affordable than other types of plastics and can be molded into complex shapes and structures. This is why injection molding is so popular for producing items like car parts, bins and storage containers.
The first step in the plastic injection process is preparing the raw materials for processing. This involves removing any moisture from the raw plastic pellets to ensure optimal performance. Then the pellets are loaded into a hopper. The hopper is connected to an injection molding machine where the pellets are heated to a melting point by a reciprocating screw. During this stage, precise temperature control is vital to achieve the desired viscosity and flow characteristics of the molten plastic.
Next, the molten plastic is injected into the hollow space of the mold through a sprue system. The sprue system is designed to guide the molten plastic into the correct positions in the mold. The injection pressure is based on the complexity of the part and the required material properties. The injection speed is also a factor in the quality of the resulting molded part.
Once the sprue system is in place, the pressure is maintained for the dwelling phase. This allows the molten plastic to fill the entire cavity of the mold. Then the sprue system is removed, and the resulting molded plastic is ejected.
During the dwelling phase, the pressure is slightly lower than the injection pressure to compensate for any material shrinkage. This step is important to ensure the part meets the specified dimensions and avoid defects such as short shots.
The type of plastic used in the injection molding process is crucial for ensuring the proper performance of the resulting product. The most common thermoplastics used in injection molding are polypropylene, polyethylene and acrylonitrile butadiene styrene (ABS). These are low-cost materials that provide an excellent balance of strength and flexibility. They are also very durable and easy to work with. Other popular thermoplastics include polyvinyl chloride, polycarbonate and nylon.
Thermosetting
Thermosetting plastics are prized for their durability and ability to withstand a wide range of chemicals. Using the injection molding process, thermoset polymers can be formed into complex shapes and dimensions that look aesthetically pleasing when finished. Depending on the application, thermosets also offer manufacturers exceptional mechanical properties. They are highly resistant to corrosion and can withstand extreme temperatures and pressure.
The injection molding process starts with raw plastic material in the form of granules or tiny pellets. This is fed through a hopper and melted under high heat in a large injector, then injected into a single or multi-cavity mould to produce the desired plastic product. The injection mould is then closed and left to cool down until the plastic is set. After the plastic has cooled, it is removed from the injection mould and can then be used in its final form. Plastic granules that are not used in the mould are recycled and ground up to create a re-grind, which can be used again in the injection process or sold to another factory for use in their manufacturing processes.
To achieve optimal results from this plastic production method, a great deal of care and attention needs to be paid to the injection molding process. Precise control is required over many factors, including injection temperature, pressure and holding time. It is also essential to use only the best quality materials. This is particularly important as it can be costly to replace a plastic injection mold.
During the injection molding process, defects can arise due to equipment-related issues. For instance, if the injection pressure is too high or the mold clamping force is insufficient, molten material will leak from the opening of the mold. This defect is called flashing. Injection molding can also be affected by uneven cooling, which leads to warping of the molded part. This can be caused by the clamping force of the injection mold, the cooling rate of the injected material or a heater malfunction. Other common injection molding problems include bubbles in the molded parts, dimensional deviations and leakage around the injection port.
Thermoforming
Thermoforming is a versatile manufacturing process that involves heating plastic to a formable state. It is widely used for a wide range of applications in the medical, retail, and consumer industries. It’s also a cost-effective option for small-scale production runs and prototypes. Unlike injection molding, thermoforming requires only a single-sided mold, and the tooling costs are much lower than those of an injection mold.
This method produces a wide variety of shapes and sizes in a short amount of time. It also allows for a high level of design flexibility, making it suitable for both large and small production runs. It is particularly useful for producing complex shapes and products with undercuts or intricate textures. This method can also be used to create inserts that are fitted into larger parts or products.
To begin the process, plastic granules or pellets are dispensed into a heated barrel. Then, a large reciprocating screw is driven by heat and pressure to melt the granules into a liquid. Once this is done, a nozzle and sprue system direct the molten plastic into a mold cavity, which can be either positive or negative in shape. The molded part is allowed to cool and solidify for about half the injection cycle, after which it can be removed from the mold.
Thermoforming is highly efficient and produces fewer defects than other processes, such as CNC machining. In addition, it can produce a number of different variations of the same product in one cycle, which reduces overall production costs. Furthermore, it is very flexible and can accommodate a wide range of different types of plastics.
While injection molding is more costly than thermoforming, there are a number of ways to reduce the cost of production. For example, reducing the complexity of a part’s design can significantly reduce the cost of creating the mold. This can also improve a product’s overall quality by eliminating unnecessary features.
Thermoforming is a popular choice for manufacturers looking to make custom plastic products that require a precise fit. Its low tooling costs, scalability, and compatibility with a variety of thermoplastic materials make it an attractive option for companies of all sizes. Thermoforming can also be used to create prototypes that allow companies to test their designs for form, fit, and function without making a significant upfront investment.
Extrusion
Injection molding is one of the most popular methods of producing plastic products. It consists of inserting plastic granules into a mold, heating and cooling them to give the product its shape. The majority of the plastic products we use today have been made using this process. It is fast and efficient, able to produce large quantities of the same product in relatively short periods of time. Injection molding’s strength lies in its ability to produce complex shapes and products with high tolerance levels. It also produces a very wide variety of products, including pipes, seals and tubing.
The plastic extrusion process is similar to injection molding but it’s used to make long, continuous shapes like tubes and wires. Unlike injection molding, extrusion doesn’t require custom-made molds. Instead, the process uses a die to shape the final product. This makes it more economical than injection molding for shorter production runs of the same product. It also has lower energy costs and can be more environmentally friendly.
It is important to note that both processes utilize raw materials in the form of plastic granules and polymer resins. These resins can be made from a wide variety of materials, depending on the application. These include ABS, clear acrylic, nylon, polyoxymethylene, polycarbonate, and thermoplastic elastomer. Both the injection molding and extrusion processes have their own strengths and weaknesses. Injection molding has the advantage of being able to work with a more diverse range of materials, but it can’t accommodate very long, thin profiles.
Regardless of the plastic molding process you choose, it’s important to test your design before production begins. This will help you to identify any flaws in the design and correct them before they become an issue during the production process. Testing will also give you a better idea of how the finished plastic part will look and feel, as well as how the runner will separate from it.